
With a vision to build a self-sustaining world, STELAPOP has devised a proprietary textile management and processing system, creating an end product that is both recycled AND recyclable - making it a circular process and product.
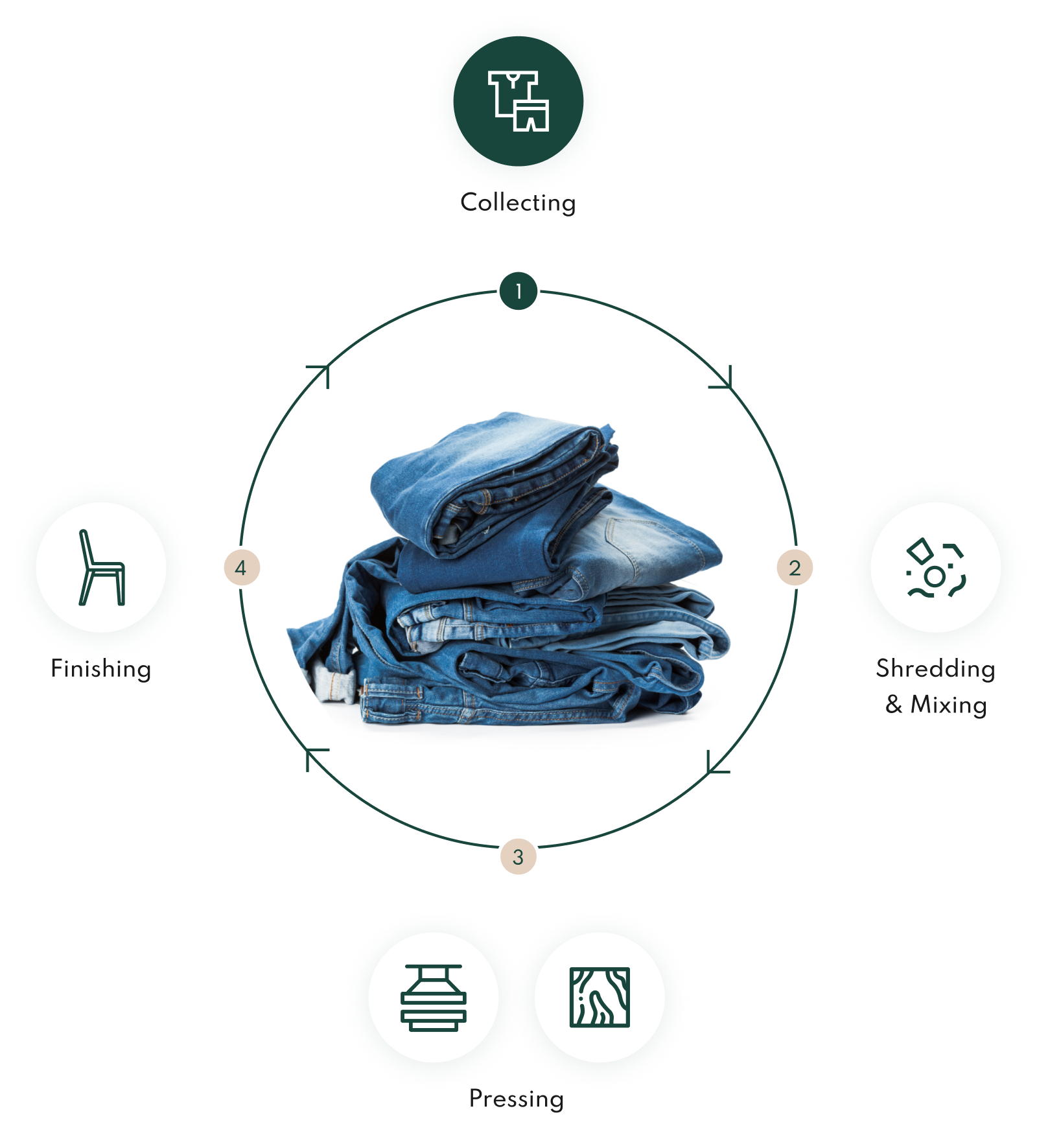
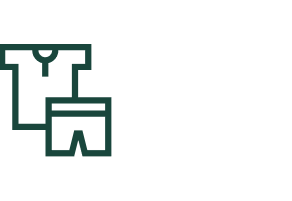
The team at STELAPOP accumulates denim waste from the partner brands and processes it. The fabric waste is then sorted and cut eliminating any additional scrap before moving to the next step.
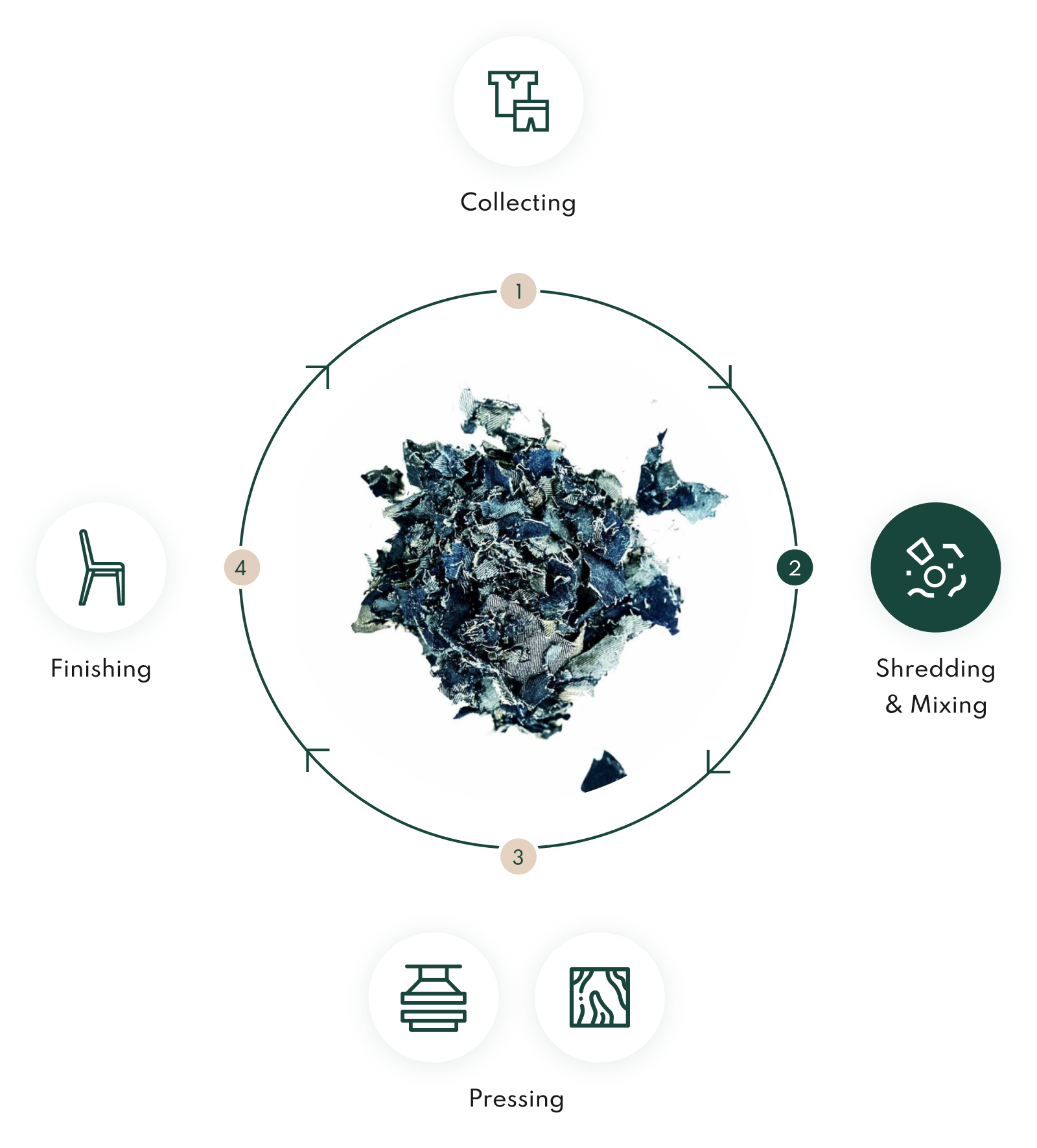
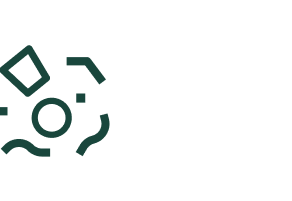
The segregating fabric waste is then mixed with our special binder in a 60:40 ratio. It is then dried out with solar energy and crushed to a fine consistency. This eco-friendly process makes it easy to upcycle the product at a later stage too.
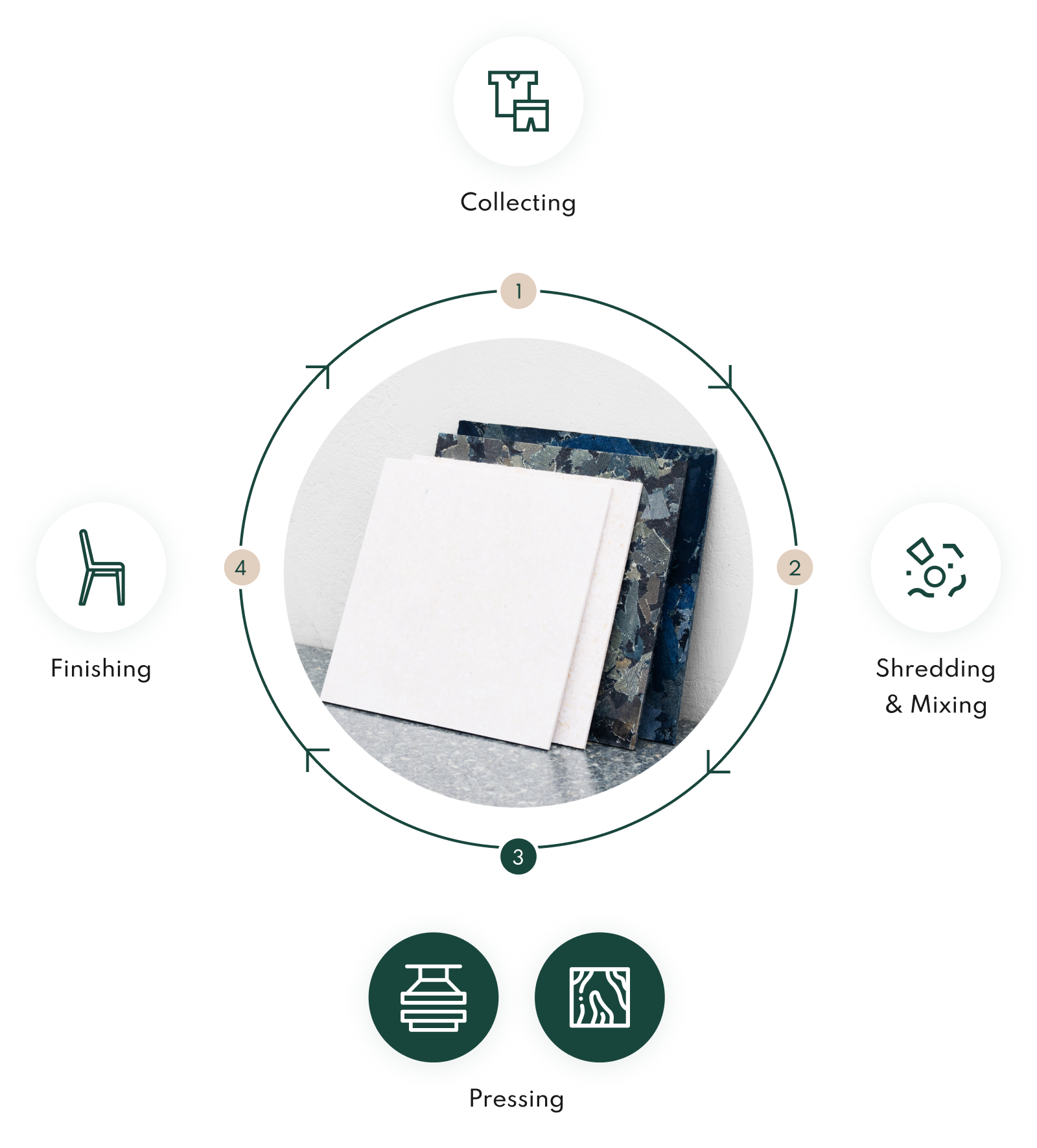
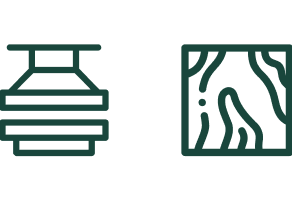
The crushed mixture is pressed and processed into woodless panels. These panels are both cold and hot pressed before being resized to different size requirements. Any wastage derived from this process can be reused upto 99% in making CORE, Reinforcement, BIO Fuel, and Bio Brick.
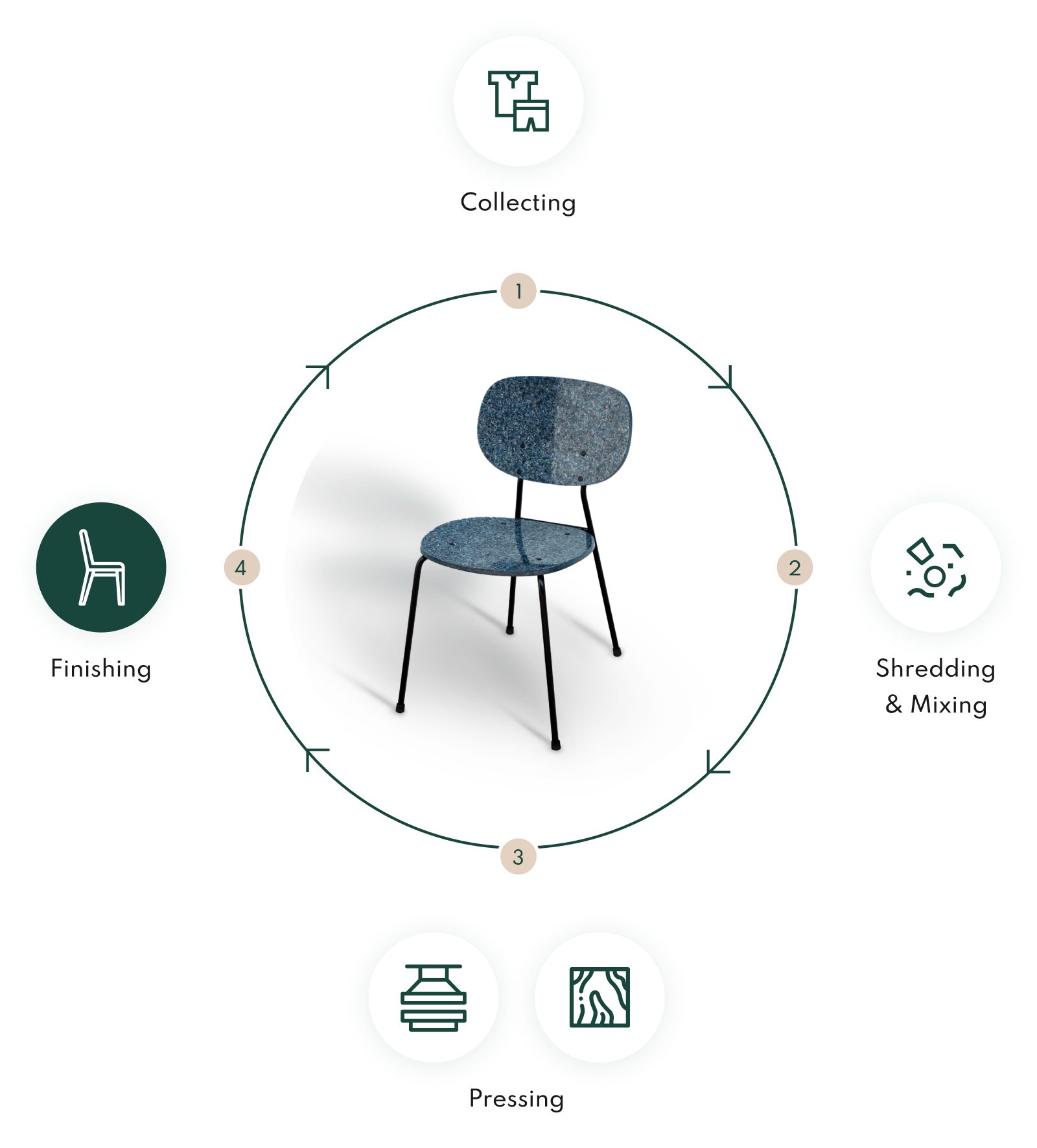

The finished panels can now we crafted into a range of woodless items like table tops, chairs, boxes, coasters, and much more.
With a vision to build a self-sustaining world, STELAPOP has devised a proprietary textile management and processing system, creating an end product that is both recycled AND recyclable - making it a circular process and product.
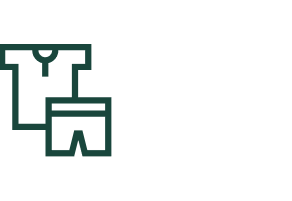
The team at STELAPOP accumulates denim waste from the partner brands and processes it. The fabric waste is then sorted and cut eliminating any additional scrap before moving to the next step.
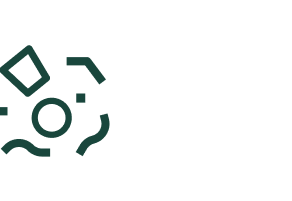
The segregating fabric waste is then mixed with our special binder in a 60:40 ratio. It is then dried out with solar energy and crushed to a fine consistency. This eco-friendly process makes it easy to upcycle the product at a later stage too.
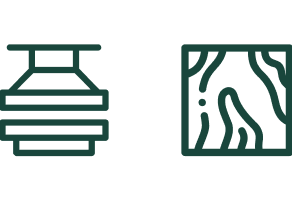
The crushed mixture is pressed and processed into woodless panels. These panels are both cold and hot pressed before being resized to different size requirements. Any wastage derived from this process can be reused upto 99% in making CORE, Reinforcement, BIO Fuel, and Bio Brick.

The finished panels can now we crafted into a range of woodless items like table tops, chairs, boxes, coasters, and much more.

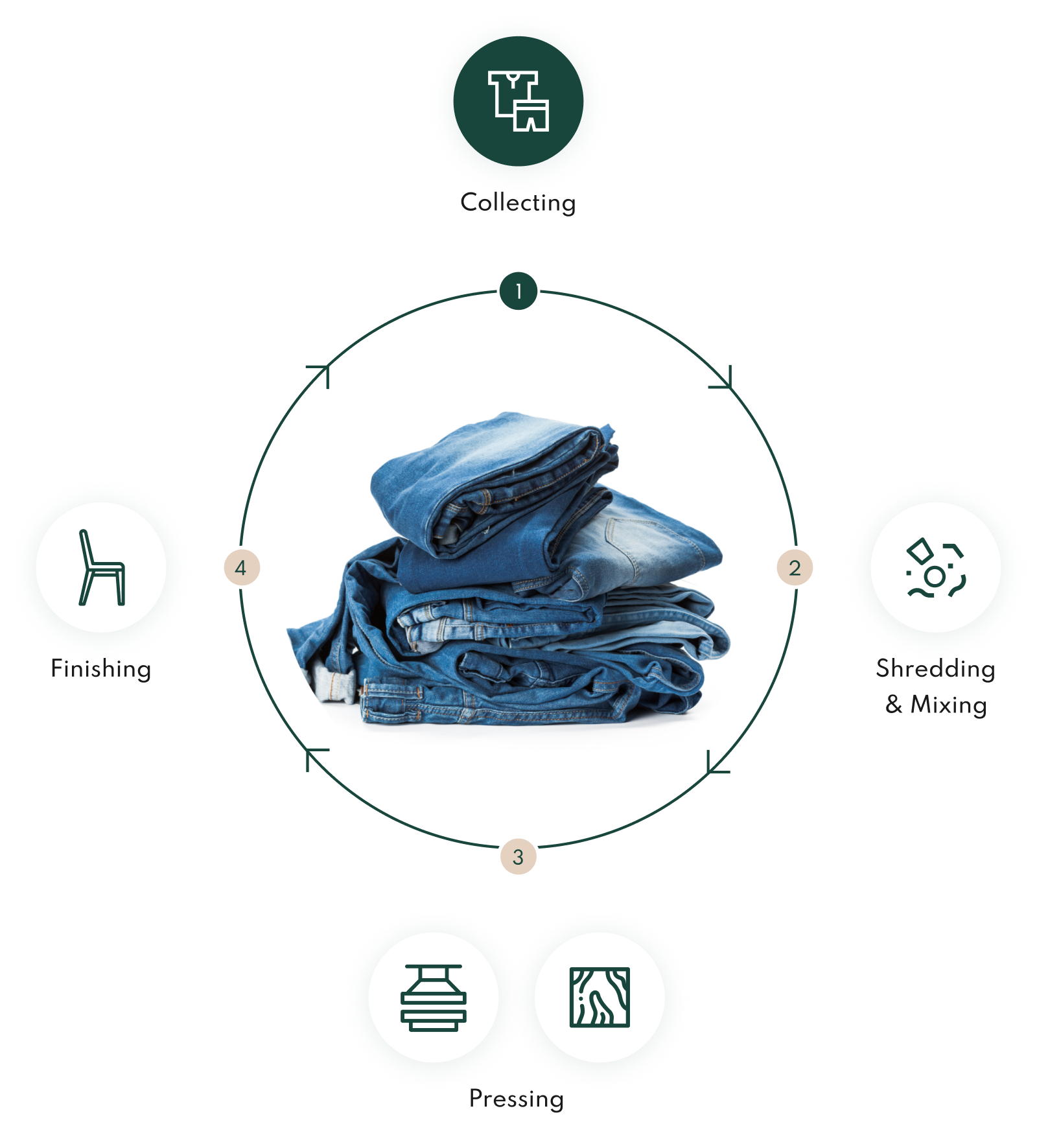
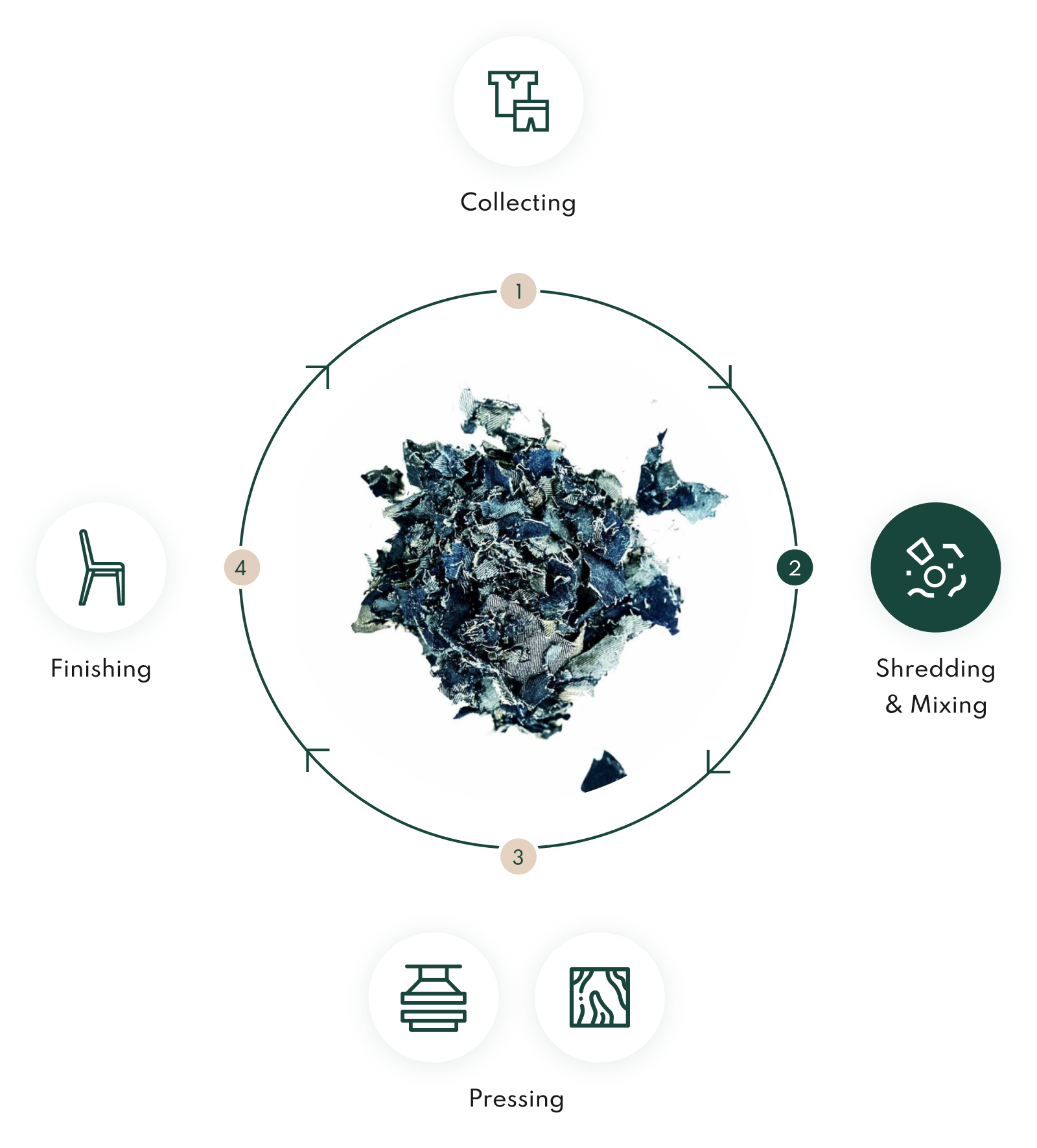
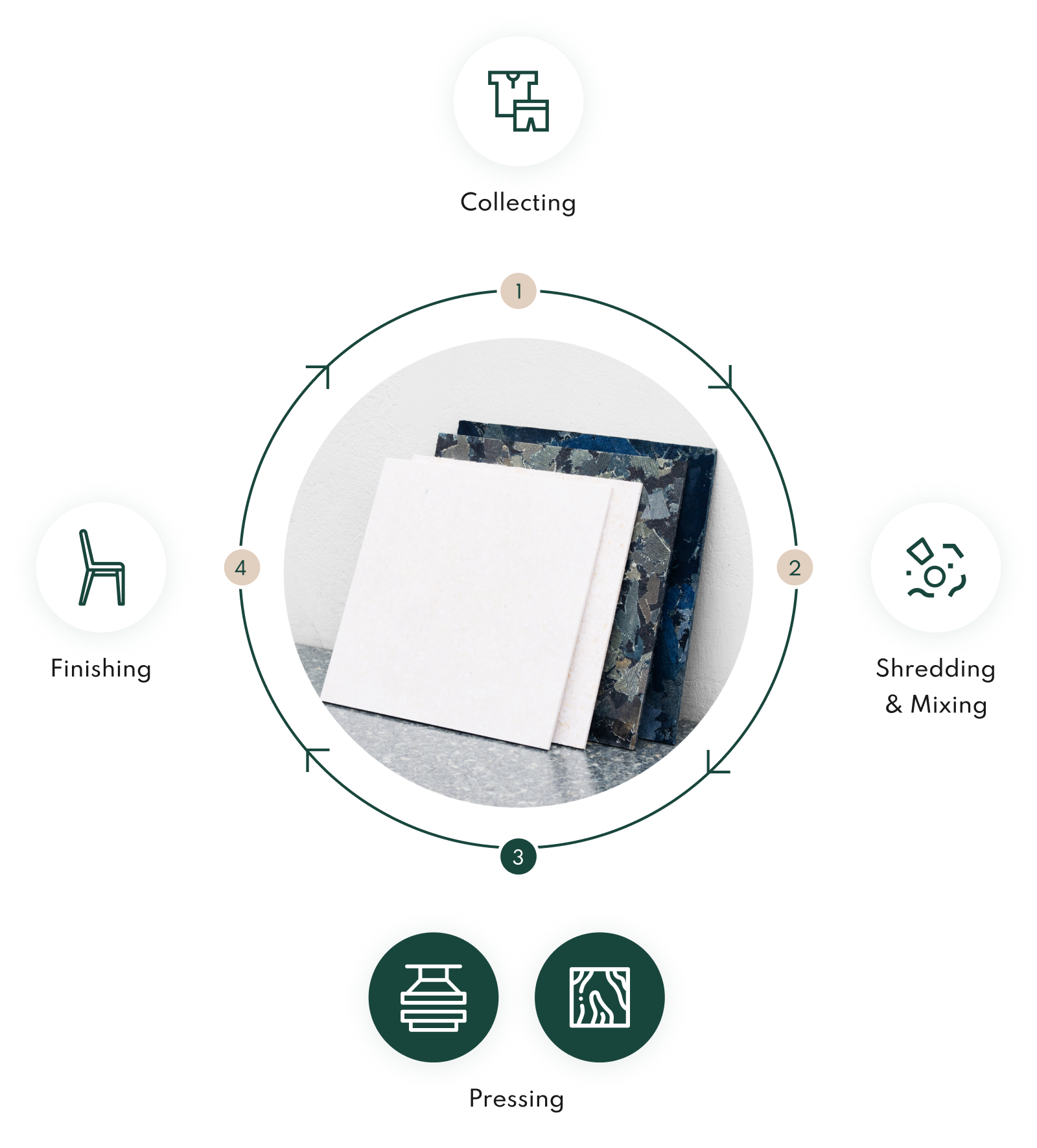
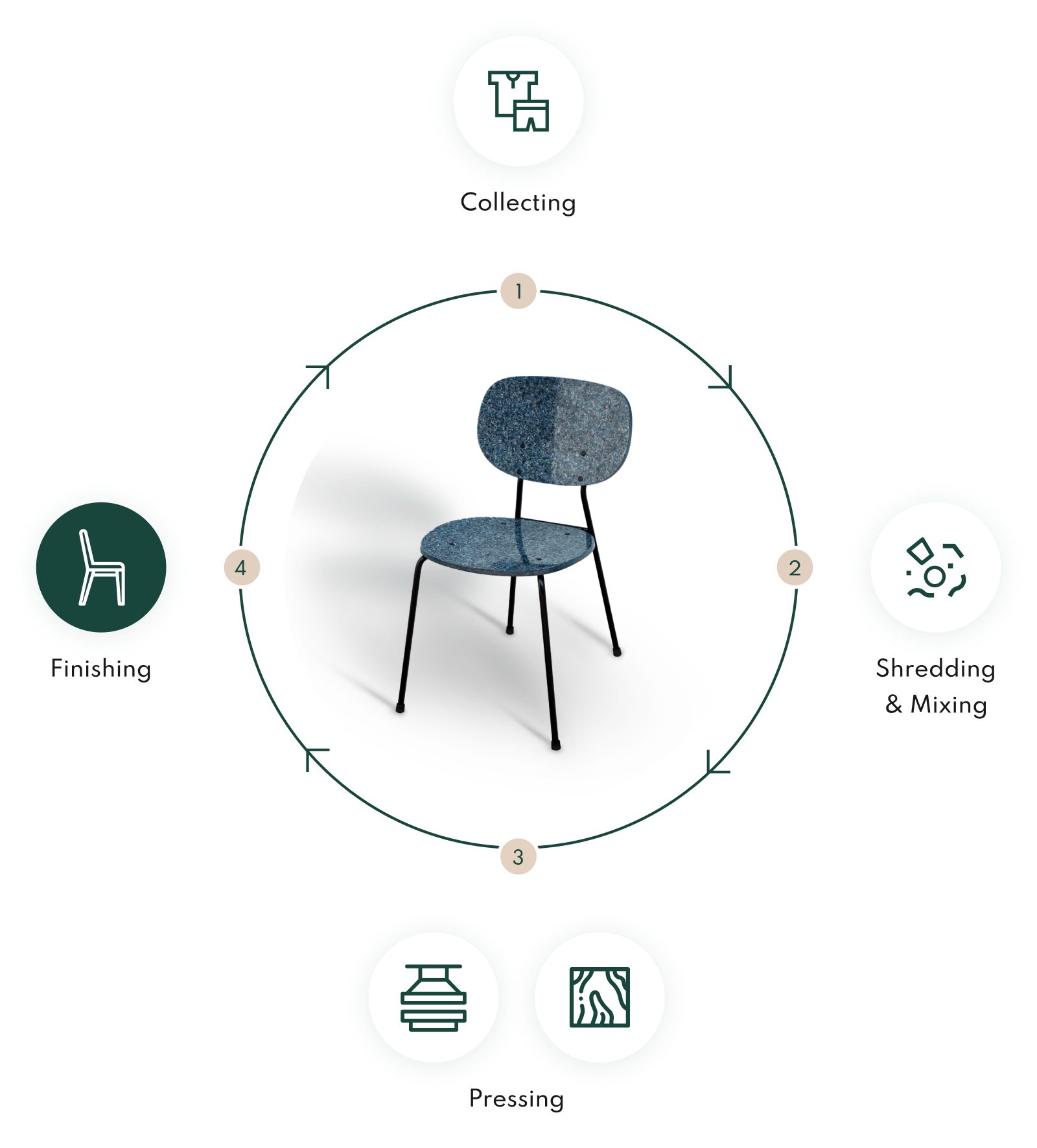







